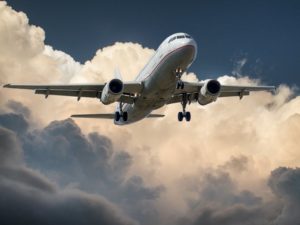
Plastics have been featured in aircrafts for decades, primarily as interior parts such as tray tables, windows, overhead bins, etc. But with the rise of modern advanced plastics, more and more critical aircraft parts are being converted from metal to plastic. That is because plastics can deliver superior aircraft parts that can withstand the harshest environments and conditions while offering increased strength and reliability.
Advanced Plastics Provide Superior Aircraft Parts
- Increased structural strength – There are numerous benefits to converting metal parts to plastic, one of which is strength. Today’s advanced plastic composites perform as well as – and sometimes better than – metal in terms of strength. Plastics tend to have both a higher strength-to-weight ratio and a higher strength-to-stiffness ratio than their traditional metal counterparts. Additionally, plastics give the option of molding in features such as ribs and gussets as the part is produced, further improving structural strength without secondary operations.
- Reduced weight – Plastic parts weigh up to 50% less than aluminum parts, and are up to 6 times lighter than steel. Reducing the overall weight of a plane means greater fuel efficiency and lower fuel costs. In fact, an airplane saves $1,000 in fuel over its lifetime for each pound of weight reduced.
- Greater design options – The flexibility of plastic allows engineers and manufacturers to design and produce complex parts, especially those that require tight tolerances. Advanced plastics are also beneficial for prototyping because they reduce the costs and time involved. Sample thermoplastic parts can quickly be produced, tested and reformed to meet modified specifications.
- Improved product life – Unlike metal parts, plastic parts don’t rust or oxidize, and many are not affected by acids or base compounds. Most advanced plastic materials have greater chemical resistance than metals, and can endure higher temperatures without warping or damage. With precision machining, plastics can hold extremely tight tolerances, ensuring optimal operation and longer product life. Self-lubricating plastics also improve part life with their extremely low wear rates, high load capacities, and lower maintenance needs.
- Eliminate costly and time-consuming secondary operations – There are numerous ways to simplify secondary operations with plastic parts. For example, plastic stock can be dyed and hot stamped with the company logo, skipping over secondary painting operations. Components can also be designed to snap together, eliminating the need for welded joints and fasteners.
Superior Aircraft Parts Are Our Specialty
At Reading Plastic, we have been producing superior aircraft parts in compliance with Aviation Standards for over 30 years. From high-performance seals and gears, to bushings, cams, and rollers, we can produce the reliable specialty parts you require. Call us today at 610-926-3245 to put our expertise to work for you.